Pipe Wall Thickness Calculation - Understand Step By Step
- April 6, 2025
- 4:07 pm
- 27000+ Comments
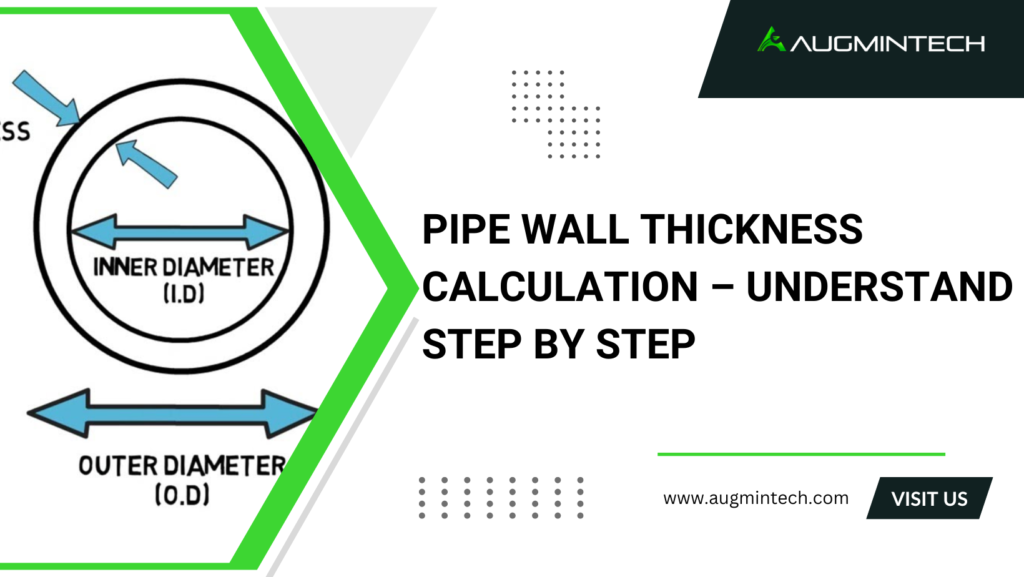
Introduction
In piping design, calculating the correct pipe wall thickness is crucial for ensuring both safety and economic efficiency. An under-designed pipe risks failure under pressure, while overdesign increases costs. One of the most commonly used methods to determine wall thickness is Barlow’s Equation, which considers internal pressure, material strength, and pipe diameter.
Whether you’re a student, a fresher, or a working design engineer, this guide will walk you through everything you need to know.
Table of Contents
What Is Pipe Wall Thickness Calculation and Why Is It Important?
Pipe wall thickness determines the mechanical strength of the pipe. It must be thick enough to resist internal pressure without rupturing. Getting this right ensures:
System safety under expected pressure and temperature conditions
Compliance with industry codes like ASME B31.3
Avoidance of unnecessary material costs
Barlow’s Equation for Pipe Wall Thickness
Barlow’s formula helps determine the minimum wall thickness of a cylindrical pipe subject to internal pressure:
t = (P × D) / (2 × S × E + P)
Where:
t = required wall thickness (mm or inches)
P = internal design pressure (MPa or psi)
D = outside diameter of the pipe (mm or inches)
S = allowable stress of the pipe material (MPa or psi)
E = weld joint efficiency factor (usually 1.0 for seamless pipe)
Example Calculation Using Barlow’s Equation
Let’s assume:
Internal Pressure (P) = 2 MPa
Outside Diameter (D) = 273.1 mm (for an NPS 10 pipe)
Allowable Stress (S) = 120 MPa
Weld Efficiency (E) = 1.0 (seamless)
t = (2 × 273.1) / (2 × 120 × 1 + 2)
t ≈ 2.27 mm
>> You should also apply a corrosion allowance (commonly 3mm) depending on the process fluid and code requirements.
Frequently Asked Questions (FAQs)
It depends on pressure, temperature, material, and corrosion allowance. Barlow’s equation helps determine it, and then you round up to the next standard pipe schedule.
Weld joint efficiency accounts for the quality of welds. For seamless pipes, E = 1. For welded pipes, it can vary between 0.6 to 0.95 depending on code and testing.
Yes, but additional stress analysis like hoop stress and flexibility analysis may be required for critical systems.
Real-Life Tips & Design Hacks
💡 1. Don’t forget corrosion allowance: Always add extra wall thickness (2–3mm) to account for material loss over time.
💡 2. Always round up to the next standard schedule: Pipe wall thickness must match available pipe schedules like SCH 40, SCH 80, etc.
💡 3. Use software like CAESAR II or AutoPIPE for large networks: These tools incorporate Barlow’s formula and code compliance checks.
💡 4. Consider temperature effects: Higher temperature reduces allowable stress, increasing the required wall thickness.
💡 5. Validate with applicable piping code (e.g., ASME B31.3): Barlow’s Equation gives the base, but codes may require safety factors or additional checks.
Ready to Master Piping Design and Become Industry-Ready?
Our Piping Design Masterclass equips you with the technical skills, calculation techniques, and code knowledge needed to thrive in the piping industry. From mastering formulas like Barlow’s Equation to understanding real-world design standards like ASME B31.3, this course is designed to take you from beginner to job-ready expert.