Pressure Drop Estimation in Piping Systems: A Complete Guide Using the Darcy-Weisbach Equation
- April 9, 2025
- 12:38 pm
- 13000+ Comments
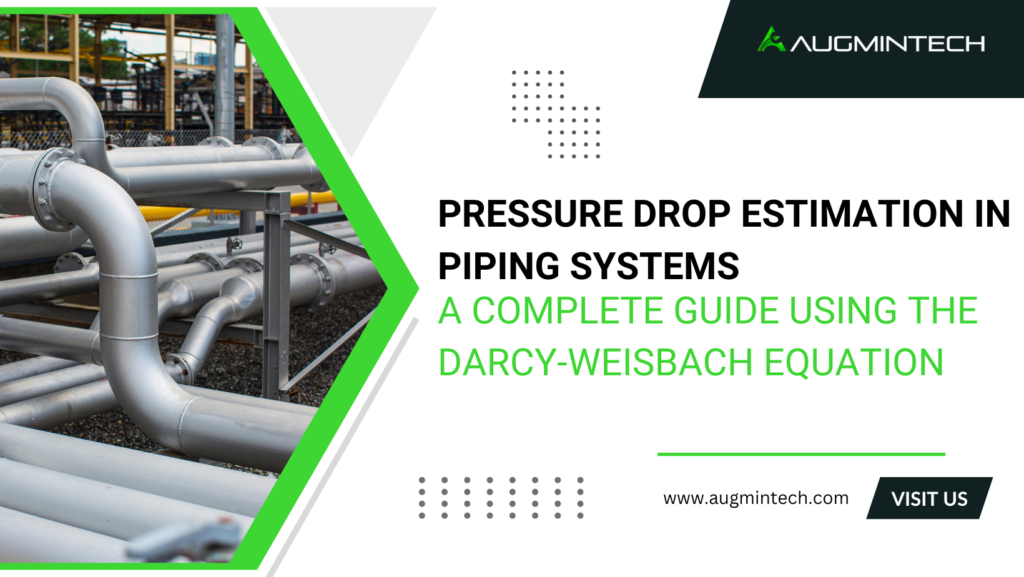
Introduction
In the world of piping design, estimating pressure drop is as critical as selecting the right material or pipe schedule. When fluid flows through a pipe, it loses energy due to friction, pipe length, diameter, velocity, and fluid properties. These losses impact pump selection, energy consumption, and overall system efficiency.
This is where the Darcy-Weisbach Equation becomes a vital tool for mechanical and piping design engineers.
Table of Contents
Darcy-Weisbach Equation Explained
The Darcy-Weisbach Equation is a universal formula used to calculate the frictional pressure loss in a straight pipe:
ΔP = f × (L/D) × (ρ × v² / 2)
Where:
ΔP = Pressure loss (Pa or N/m²)
f = Friction factor (dimensionless)
L = Length of the pipe (m)
D = Internal diameter of the pipe (m)
ρ = Fluid density (kg/m³)
v = Flow velocity (m/s)
Frequently Asked Questions (FAQs)
A significant pressure drop can lead to pump inefficiencies, poor system performance, or even equipment damage. Estimating pressure drop accurately ensures your system is both functional and energy-efficient.
The friction factor depends on the Reynolds number and pipe roughness. It can be determined from the Moody chart or formulas like Colebrook-White or Swamee-Jain equations.
It’s best suited for turbulent and fully developed flow in circular pipes. For laminar flow (Re < 2000), the friction factor can be directly calculated as:
f = 64 / Re
Engineering tools like AFT Fathom, CAESAR II, or Excel-based calculators help streamline pressure drop estimations for complex systems.
Example Calculation
Let’s assume:
Pipe Length (L) = 50 meters
Pipe Diameter (D) = 0.1 m
Fluid Density (ρ) = 1000 kg/m³ (water)
Flow Velocity (v) = 2 m/s
Friction Factor (f) = 0.02
ΔP = 0.02 × (50 / 0.1) × (1000 × 2² / 2)
ΔP = 0.02 × 500 × (2000 / 2)
ΔP = 0.02 × 500 × 1000 = 10,000 Pa (or 10 kPa)
This means the pump must overcome a 10 kPa pressure loss due to friction alone.
Real-Life Hacks & Design Tips
💡 1. Minimize elbows and fittings: Bends and valves add additional pressure losses. Use long-radius bends where possible.
💡 2. Keep pipe diameter optimal: Oversized pipes are expensive; undersized ones increase friction loss. Use velocity and Reynolds number to strike a balance.
💡 3. Use pipe material wisely: Smooth pipes (e.g., PVC, stainless steel) have lower friction factors than rougher ones (e.g., cast iron).
💡 4. Account for elevation changes: Static head from elevation differences also adds to total pressure requirements.
💡 5. Automate with software tools: Use piping system design tools to include minor losses (like valves and tees) using equivalent length or K-factors.
Conclusion
Pressure drop estimation is a cornerstone of efficient piping design. Ignoring it could result in oversized pumps, energy waste, or even system failure. By mastering the Darcy-Weisbach equation, you ensure your designs are both reliable and optimized for performance.
Whether you’re designing HVAC, water treatment, chemical, or oil & gas systems—pressure loss matters.
Ready to Master Piping Design and Become Industry-Ready?
Our Piping Design Masterclass equips you with the technical skills, calculation techniques, and code knowledge needed to thrive in the piping industry. From mastering formulas like Barlow’s Equation to understanding real-world design standards like ASME B31.3, this course is designed to take you from beginner to job-ready expert.